Although with a certain phase shift, the further development of underwater explosives to combat surface vessels and submarines proceeded congruently with the perfection of their defence measures. The principle became established that the use of sea mines and sea mine defence were mutually dependent.
In the decades that followed, various means of sea mine defence were developed: trailed mechanical clearing devices for cutting anchor mines, trailed electrodes and sound generators that were designed to respond to the sensors of bottom mines and, finally, sonar systems that enable the detection of dangerous objects in the water column and on the seabed. In the case of sonar-supported mine hunting, the mines are destroyed using mostly wire-guided underwater drones or by mine divers. One speciality is the Troika system, in which remote-controlled surface drones of the Seehund type simulate an acoustic and magnetic field of a much larger ship, to which the sensors of modern sea mines respond.
As a result, numerous sea mine defence techniques have been developed, which are used depending on the threat and environmental conditions. This mix of sonar-supported mine hunting, ship field-simulating mine sweeping and mine diving is known as combined sea mine defence. It is represented in the German Navy by the 332 boat class, which has the specific equipment on board in three different modifications (332 C, 332 CL, 332 B).
Threat
Sea mines have the potential to create threats in sea areas, increasing the risk of damage when travelling in these areas. This means that sea mines can change maritime geography, as areas that could be mined must be avoided.
A wide range of different mines are available. Anchor mines are deployed when their horns come into contact with the hull of a ship. Ground mines placed on the seabed react to changes in the earth's magnetic field, acoustics and pressure conditions when a vehicle passes over. They move directly or work through counting steps in order to explode only when a previously defined overrun occurs. Modern sea mines may even be mobile and dig themselves in to make themselves undetectable by sonar. The same purpose is served by the use of materials that improve their stealth qualities. Overall, sea mines open up a wide range of possibilities in warfare, both on the bottom and in the water column, thanks to their highly specialised sensor technology and the combination of their sensory elements.
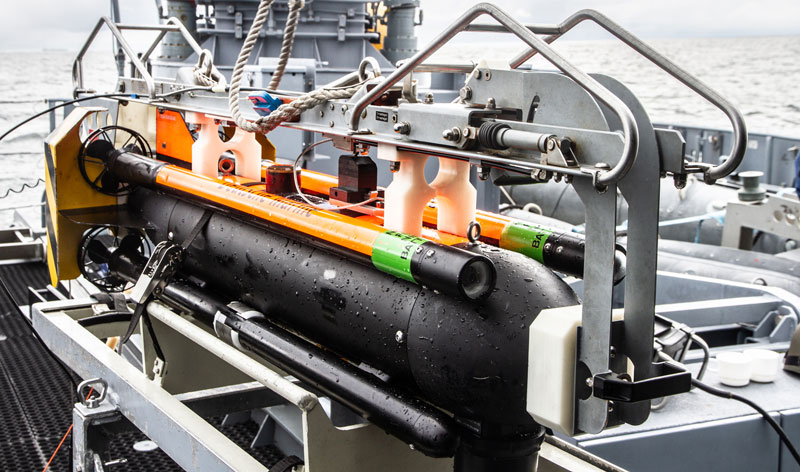
A Seefuchs drone on board the M 1059 Weilheim minehunter. Photo: Bundeswehr/Marcel Kröncke
Boat classes
The German Navy has built up decades of expertise in deploying and combating sea mines. The two disciplines have always been inextricably linked. After the end of the Cold War, the fleet of around 70 mine defence vessels was gradually reduced to such an extent that only ten boats are still available today:
Five Class 332C boats that detect and classify mines using a hull-mounted minehunting sonar. Subsequently, any necessary countermeasures are carried out using Seefuchs drones or mine divers.
Three Class 332CL boats, which also hunt mines and can carry up to four Seehund-type clearance drones in the minefield.
Two 332B minesweepers, which utilise the special skills of minesweepers from the high seas to the beach. They are supported by autonomous underwater vehicles.
All boats are highly protected: By using non-magnetic shipbuilding steel, non-magnetic system components and corresponding propulsion systems, their magnetic and acoustic signature is reduced so that they can operate protected in the minefield. This is necessary because, on the one hand, the boundaries of a minefield can never be identified with one hundred per cent certainty and, on the other, the boats have to enter the minefield to relocate and combat sea mines.
In their entirety, the boats, distributed across the classes, represent the connected sea mine defence. The focus is on mine hunting: only when environmental conditions do not permit or restrict this is simulated minesweeping used. This is how hunt where you can, sweep where you must became the structuring principle for naval mine defence in the German Navy. Sea dogs and, in future, autonomous underwater vehicles as sonar carriers will allow the mine defence unit to stay out of the minefield as far and as long as possible. Should a stay in the minefield be unavoidable, the protected boats will allow operations in the minefield.
Capability gap
The Class 332 units commissioned between 1993 and 1998 will reach the end of their service life towards the end of the decade. Obsolescence of various system components means that these units cannot be kept operational without considerable effort. The project management at BAAINBw ensures that the operational readiness of the units can be maintained, but this will only be possible at great technical and financial expense as the boats get older. It has therefore been planned that successor units will be put into service from the end of the decade.
There has also been a change in the way they are used. The boats were developed and built in the 1980s for use in the North Sea and Baltic Sea. The hull shape and mine sonar were optimised for this purpose. Since the end of the 1990s at the latest, the area of operation has also been extended to the European marginal seas. The environmental conditions there differ considerably from those in domestic waters.
Capabilities that were performed by other units in the formation, such as defence against aircraft or electronic reconnaissance and corresponding countermeasures, have never been implemented on the Class 332, or only very weakly. In current and future scenarios, the focus on sea mine defence is no longer sufficient.
What's more, the technological trend in sea mine defence is moving in the direction of locating and combating sea mines at a distance. This means that unmanned surface and underwater vehicles are deployed autonomously in mine-prone areas. The units that operate these autonomous drones remain far outside the minefield and only enter it when necessary. The principle here is: unmanned where you can - manned where you must.
Future capability carrier for connected sea mine defence
Maintaining the capability for sea mine defence is essential, as it is what makes the development of other capabilities in the maritime dimension possible in the first place. A future naval mine countermeasures capability must therefore ensure linked naval mine countermeasures, whereby sonar-based mine hunting remains the main task, be highly protected and robust, be able to independently counter threats from the air and above water, participate in and contribute to the situation picture, not just the underwater situation picture relating to sea mines, and be able to act at a distance.
The Maritime Mine Countermeasures New Generation (MMCM NG) project set up by the European Defence Agency (EDA) at Germany's initiative in 2013 with the participating nations of Belgium, Estonia, Sweden, Norway and the Netherlands was aimed at analysing and coordinating requirements and planning the maintenance of sea mine countermeasures capabilities within a multinational framework.
In 2014, the Naval Command also developed the Specialised Mine Countermeasures Capability Carrier initiative on the basis of the results achieved up to that point in the EDA project. It contains the capabilities described above for the future mine countermeasure units. At the same time, the use of flexible sea mine defence modules that can also be deployed from other capability carriers was described, as well as intensive usability with a reserve for future technologies.
The EDA's work in the MMCM NG project gave new impetus to the preservation of sea mine defence capabilities. The Preliminary Planning Instruction 2020 already called for the preservation of the capability to defend against sea mines and explosive ordnance in the maritime environment. The Supplementary Planning Directive 2017 underpinned the maintenance and expansion of capabilities by calling for unmanned and remote-controlled detection of explosive ordnance and mines. The requirement is reaffirmed in the medium-term financial planning for 2022.
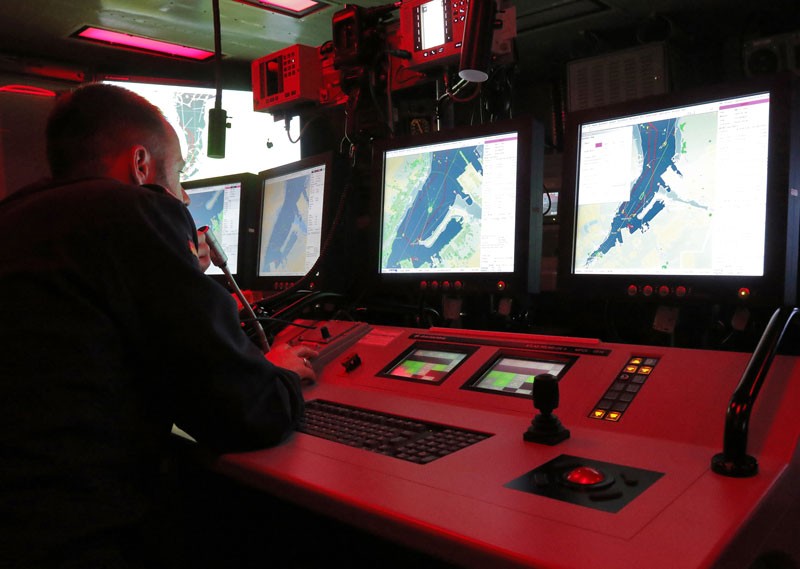
The operations centre of the Grömitz minehunting boat. Photo: Bundeswehr/ Björn Wilke
Results of the first analysis phase
In August 2017, the Ministry of Defence commissioned the creation of the Capability Gap and Functional Requirement (FFF) document. It was produced with great commitment within a year. In addition to the document itself, which is purely descriptive and discusses the background, the prioritised list of requirements (PFK) is of crucial importance for further project work. Here, the requirements were divided into the capability domains of leadership, education, impact and support. There were also considerations on cross-sectional requirements and demands on the mission components.
The future mine defence vehicle must participate actively and passively to the full extent in the situation picture of the tactical level in the sea and air dimensions, and also on land in the case of coastal operations. It should contribute to and participate in the situation picture for its own and allied forces. In addition, it should be able to accommodate the staff of a commander and ensure his command capability.
In the theatre of operations, the capability carrier must use its own sensors to reconnoitre the situation above and under water. The high quality of the reconnaissance is decisive for the units that operate remotely. The capability dimension is flanked by electronic warfare and electronic protection measures.
In addition to mine defence, the capability carrier must also be able to defend against asymmetric threats from the air and over water. It has a basic minehunting capability, is technically designed to accommodate mine divers and can deploy unmanned surface and underwater systems.
In order to increase the flexibility of the connected naval mine defence system and to be able to react to technological developments in the future, the basic capability carrier is supplemented by mission components. These include extended mine hunting with remote, unmanned surface and underwater systems, drift mine countermeasures and combating camouflaged, silted-up and washed-in mines, mine clearance by unmanned vehicles, extended mine diving capabilities and the ability to deploy mines.
Apart from mine deployment and mine clearing, these components can also be made available as modules to other capability carriers and for land-based operations.
In the area of cross-sectional capabilities, it is required that a low signature is guaranteed, that a given speed profile is maintained in formation and individual travel and that the ability to grow over the lifetime is given.
Second analysis phase
The second part of the analysis phase began with the approval of the FFF in January 2021 and is being carried out by the project unit for mine defence vehicles in the BAAINBw. The first step is to compare the results of numerous investigations from the first analysis phase, both within the national and DFA framework, with the requirements of the PFK in order to identify any further need for investigation. The proposed solutions then form the technical assessment of the functional and operational requirements, which in turn must be approved by the Inspector General of the Bundeswehr as part of the so-called selection decision. Only with this decision will it be possible to establish the financial requirements in Section 14. The competition for the new construction of the mine defence units will then take place between 2024 and 2025. If a construction contract can be concluded in 2025, the first new unit can be expected to arrive at the end of this decade.
Author: Frigate Captain Thomas Klinke is Head of Overall Integration of Unmanned Underwater Vehicles at the Federal Office of Bundeswehr Equipment, Information Technology and In-Service Support.
PEGASSSO.